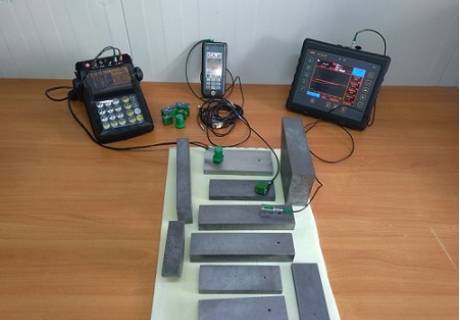
Для чего проводят ультразвуковой контроль
Ультразвуковой контроль сварных соединений и основного металла – одна из обязательных процедур при техническом диагностировании, отражённая во многих руководящих документах, от РД РОСЭК-004-97 до СТО Газпром 2-2.3-066-2006. Применение УЗК привлекательно тем, что не предполагает разрушения объекта. Даже остановки эксплуатации, как правило, не требуется. Это особенно важно, например, для диагностики трубопроводов, когда нет возможности их дренировать. Отчасти именно поэтому ультразвуковой контроль всё чаще противопоставляют радиографическому. В пользу первого говорит ещё и то, что он безвреден для человеческого здоровья. Приборы для УЗК хороши своей портативностью, удобство работы в полевых условиях, большим многообразием датчиков, призм, сканеров и прочих принадлежностей для самых разных задач дефектоскопии.
Что касается недостатков этого метода, то чаще всего к ним относят:
- существенные ограничения при сканировании материалов с крупнозернистой структурой и высоким коэффициентом затухания. Это объясняется слишком интенсивным рассеиванием колебаний. К таким «проблемным» материалам относятся, например, чугун и сплавы с повышенным содержанием никеля;
- сложность при проведении контроля соединений разнородных материалов;
- ограниченная пригодность к дефектоскопии объектов сложной конфигурации;
- относительно низкая точность при оценке реальных размеров дефектов (данная проблема успешнее решена в технологиях ФР и TOFD, о которых написано ниже).
На каких объектах практикуется ультразвуковой контроль
Метод ультразвукового контроля практикуется едва ли не во всех отраслях промышленности, от нефте- и газоперерабатывающих производств до атомной энергетики. В металлургии его используют для отбраковки литья и поковок. В авиа- и судостроении – для проверки композитов, сотовых структур, полимеров на предмет трещин, непроклеев и пр.
Вот лишь несколько примеров объектов, на которых проводится УЗК:
- магистральные и технологические трубопроводы газа, пара, нефти, нефтепродуктов и прочих рабочих сред;
- оболочки реакторных установок;
- рельсы, стрелочные переводы;
- литые детали тележек грузовых вагонов;
- обшивка сосудов, работающих под давлением;
- корпуса насосов и многое-многое другое.
Ультразвуковой контроль сварных соединений и основного металла эффективен для выявления развивающихся дефектов, возникших в результате эксплуатации. Именно поэтому его проводят не только для входного и выходного контроля, но и для последующих обследований и технических освидетельствований. Без проведения УЗК и/или толщинометрии (УЗТ) не обходится ни одна полноценная экспертиза промышленной безопасности сосудов, работающих под давлением, магистральных и технологических трубопроводов, арматуры, теплообменников, печей и т.д.
Оформить заявку
Закажите ультрозвуковой контроль (УЗК) в нашеё Лаборатории Неразрушаемого Контроля, заполнив эту форму
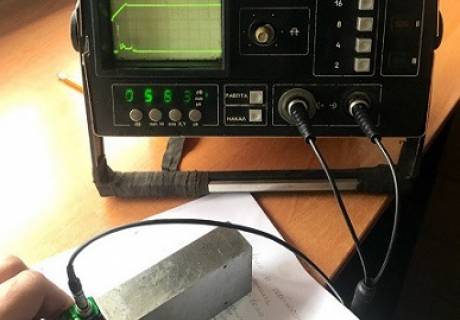
Виды ультразвукового контроля
В ГОСТ 23829-85 приводятся определения 16 различных методов УЗК. Мы перечислим лишь основные, наиболее распространённые на практике:
- теневой. По обе стороны сварного шва, перпендикулярно к его поверхности устанавливаются два преобразователя, один выполняет функцию излучателя, второй служит приёмником. При наличии инородной среды образуется глухая зона, что позволяет судить о наличии дефекта;
- эхо-импульсный. Метод очень распространён для ультразвукового контроля сварных соединений. Дефектоскоп одновременно и возбуждает, и принимает упругие волны. Если они беспрепятственно проходят через материал и не отражаются, значит, причин для отбраковки нет. В противном случае возникает эхо-сигнал, что свидетельствует о наличии отражателей – неоднородностей. Способ привлекателен тем, что подходит для объектов с односторонним доступом, не требует снятия усиления и иных сложных подготовительных мероприятий;
- эхо-зеркальный. Излучатель и приёмник разделены и расположены по одну сторону от исследуемого объекта. Волны излучаются под углом и, отражаясь от дефектов, фиксируются приёмником. «Тандем» как метод ультразвукового контроля особенно эффективен для выявления дефектов, перпендикулярных сварному соединению. В первую очередь – речь идёт о трещинах;
- зеркальной-теневой. Отличается от обычного теневого тем, что преобразователи находятся на одной стороне относительно исследуемой поверхности. Косые волны отражаются от противоположной стороны сварного шва. Если приёмник не фиксирует отражённый сигнал, значит, имеется дефект;
- дельта-метод. Данный вид ультразвукового контроля применяется редко – когда к качеству сварных соединений предъявляются особо жёсткие требования. Технология предполагает трудоёмкую, очень тонкую настройку дефектоскопа. Расшифровка результатов требует от специалиста особой подготовки. При всех недостатках у этого метода есть очень важное преимущество – повышенная чувствительность к вертикально-ориентированным трещинам, не всегда доступным для выявления стандартным эхо-методом. Суть дельта-метода в том, чтобы определить энергию колебаний, отражённых от дефекта внутрь сварного шва;
- велосиметрический. Основан на том, чтобы зафиксировать и
проанализировать изменение скорости колебаний в дефектной зоне. Обычно
применяется для композиционных материалов;
ревербационно-сквозной. Также используется для ультразвукового контроля композитных, полимерных и многослойных материалов. Излучатель и приёмник располагаются по одну сторону объекта, на небольшой дистанции друг от друга. Волны посылаются в материал и после многократных отражений «добираются» до приёмника. Стабильные отражённые сигналы свидетельствуют об отсутствии дефекта. В противном случае наблюдается изменение амплитуды и спектра принятых сигналов.
Разумеется, изложенный перечень – далеко не исчерпывающий. При этом все перечисленные выше методы ультразвукового контроля сварных соединений и основного металла относятся к категории активных. Каждый из них подразумевает искусственное излучение и приём акустических волн, которые осуществляются при помощи специальной аппаратуры. Другое дело – пассивные методы. Самый яркий «представитель» этой категории – акустико-эмиссионный мониторинг, но это, по факту, отдельное направление акустической дефектоскопии.
Ультразвуковой контроль сварных соединений: последовательность действий
В классическом виде акустическая дефектоскопия включает в себя следующие этапы:
- зачистку металлической поверхности – сварного шва и околошовной зоны – от краски, ржавчины, окалины, загрязнений;
- калибровку и настройку дефектоскопа;
- непосредственное прозвучивание объекта. Прижимая датчик к поверхности, оператор выполняет продольно-поперечные и вращательные движения;
- сохранение результатов, передача на ПК;
- расшифровку данных, оформление заключения.
На каких объектах практикуется ультразвуковой контроль
Метод ультразвукового контроля практикуется едва ли не во всех отраслях промышленности, от нефте- и газоперерабатывающих производств до атомной энергетики. В металлургии его используют для отбраковки литья и поковок. В авиа- и судостроении – для проверки композитов, сотовых структур, полимеров на предмет трещин, непроклеев и пр.
Вот лишь несколько примеров объектов, на которых проводится УЗК:
- магистральные и технологические трубопроводы газа, пара, нефти, нефтепродуктов и прочих рабочих сред;
- оболочки реакторных установок;
- рельсы, стрелочные переводы;
- литые детали тележек грузовых вагонов;
- обшивка сосудов, работающих под давлением;
- корпуса насосов и многое-многое другое.
Ультразвуковой контроль сварных соединений и основного металла эффективен для выявления развивающихся дефектов, возникших в результате эксплуатации. Именно поэтому его проводят не только для входного и выходного контроля, но и для последующих обследований и технических освидетельствований. Без проведения УЗК и/или толщинометрии (УЗТ) не обходится ни одна полноценная экспертиза промышленной безопасности сосудов, работающих под давлением, магистральных и технологических трубопроводов, арматуры, теплообменников, печей и т.д.
Дефектоскопы и другое оборудование для ультразвукового метода контроля
Современные дефектоскопы хороши не только своей портативностью, удобством применения в полевых условиях и на большой высоте. Гораздо важнее – обширный набор функций и многообразие индивидуальных пользовательских настроек. В зависимости от модификации УЗК-дефектоскоп может отображать на своём дисплее А-, В-, С-, S-, L-сканы, вплоть до построения 3D-моделей профиля изделий.
Заканчивая этот блок, нельзя не сказать и об ультразвуковой толщинометрии (УЗТ). Измерение толщины металла – один из ключевых способов коррозионного мониторинга. По результатам УЗТ можно судить об остаточном ресурсе конструкции (механизма, оборудования и пр.).
Как и в ультразвуковом контроле, принцип построен на использовании импульсов, которые излучает преобразователь. Прибор измеряет скорость, за которую они проходят через стенку. Если конкретнее, то известно 3 основных режима:
- однократного эхо-сигнала. Измеряется время, которое проходит между начальным импульсом возбуждения и первым эхо-сигналом. Значение корректируется с учётом толщины протектора ПЭП, компенсации степени изнашивания и слоя контактной среды;
- однократного эхо-сигнала линии задержки. Измеряется время от конца линии задержки до первого донного эхо-сигнала;
- многократных эхо-сигналов. Измеряется время прохождения между донными эхо-сигналами.
Наиболее продвинутые модели имеют два и более независимых канала. Технически самыми совершенными считаются многоканальные приборы со специальным ПО и поддержкой секторного и/или линейного сканирования.
Речь идёт о двух технологиях ультразвукового контроля сварных соединений:
- фазированных решётках (ФР). Имеются в виду особые датчики (кристаллы), на поверхности которых с определённым шагом расположены 16, 32, 64 или 128 элементов. Каждый из них излучает волны с определённой задержкой. Корректируя этот «сдвиг по фазе», можно получить фронт волны с определённым углом. В этом и заключается принцип секторного сканирования. Оператору не нужно водить датчиком по поверхности – он и без этого «видит» все дефекты, расположенные в заданной зоне. По сравнению с одноэлементными ПЭП фазированные решётки могут генерировать пучок волн точно в зоне дефекта. В режиме реального времени на экране многоканального дефектоскопа выстраиваются наглядные А-сканы, на основе которых формируются детализированные, информативные отчёты. Мёртвая зона минимальна. Производительность ультразвукового контроля с ФР примерно в 3–4 раза выше, чем у традиционного УЗК;
- дифракционно-временном методе (Time of Flight Diffraction, сокращённо – TOFD). Суть технологии – регистрация поперечных и продольных (боковых) волн, дифрагированных на краях несплошностей. Метод предполагает использование двух наклонных датчиков для излучения и приёма волн, расположенные по обе стороны сварного шва. «Натыкаясь» на дефект, волны изменяют своё направление и время прохода. Последний показатель в режиме TOFD считается ключевым. Дифракционно-временной метод эффективно выявляет точечные дефекты, выходящие на поверхность трещины, вогнутость, непровары в корне, расслоения, питтинговую коррозию и пр. Точность измерений достигает ±1 мм. Повторяемость результатов приближается к 100%. По своей информативности и достоверности линейное сканирование – полноценная замена радиографическому методу, особенно для дефектоскопии низколегированных и нелегированных углеродистых сталей.
Другой важнейший атрибут для ультразвукового контроля качества сварных соединений – это преобразователи. Они же датчики, они же ПЭП. Состоят из призматической искательной головки и пластины, изготовленной из титанита бария либо кварца. После того, как на неё подаётся ток в диапазоне частот 0,8–2,5 МГц, начинается излучение коротких импульсов упругих колебаний. Современные датчики позволяют корректировать их длительность и временной интервал между ними.
ПЭП различаются по углу ввода колебаний, способу излучения и приёма ультразвукового тракта, типу контакта, форме акустического поля и рабочей поверхности.
Для ультразвукового метода контроля сварных соединений используются преобразователи следующих типов:
- совмещённые, раздельные и раздельно-совмещённые;
- прямые, наклонные, комбинированные и с переменным углом ввода;
- фокусирующие и нефокусирующие;
- притёртые и непритёртые;
- контактные, иммерсионные, бесконтактные, щелевые и т.д.
Датчики для ультразвукового дефектоскопа
Образцы для настройки перед проведением ультразвукового контроля
Помимо этого, в УЗК активно применяются различные призмы, координатные
устройства и сканеры. Для настройки и калибровки не обойтись без
стандартных образцов (СОП, СО) и настроечных мер. Для улучшения
акустического контакта на поверхность объекта предварительно наносят
контактную жидкость/гель.
Для проведения УЗТ требуется толщиномер. Такой прибор технически проще, компактнее, дешевле классического дефектоскопа.